The Science Behind Porosity: A Comprehensive Overview for Welders and Fabricators
Comprehending the complex mechanisms behind porosity in welding is crucial for welders and fabricators striving for impeccable workmanship. From the composition of the base materials to the ins and outs of the welding procedure itself, a plethora of variables conspire to either exacerbate or ease the presence of porosity.
Comprehending Porosity in Welding
FIRST SENTENCE:
Exam of porosity in welding exposes critical understandings right into the honesty and quality of the weld joint. Porosity, characterized by the presence of cavities or spaces within the weld metal, is a typical problem in welding procedures. These gaps, if not appropriately resolved, can compromise the architectural stability and mechanical buildings of the weld, leading to prospective failures in the finished product.

To spot and quantify porosity, non-destructive testing techniques such as ultrasonic testing or X-ray inspection are usually used. These strategies enable the identification of internal defects without jeopardizing the honesty of the weld. By examining the size, shape, and circulation of porosity within a weld, welders can make educated choices to boost their welding procedures and achieve sounder weld joints.
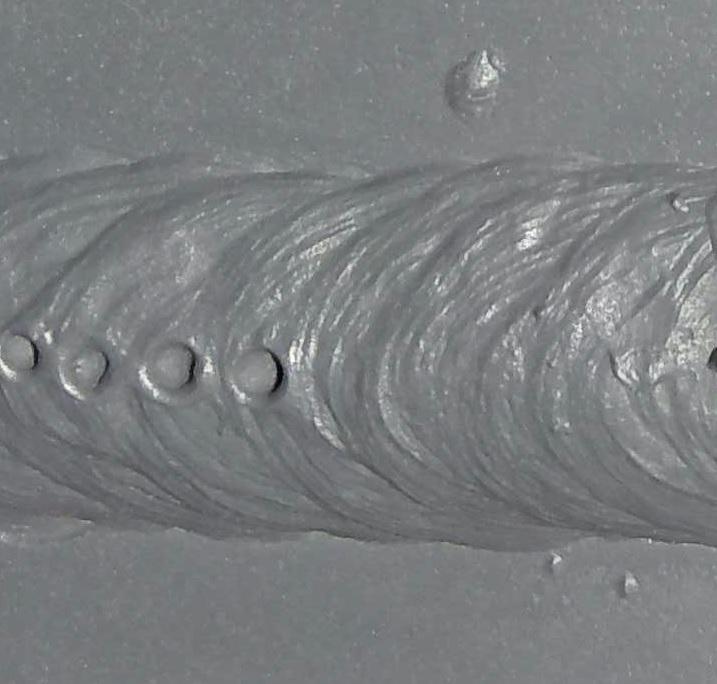
Factors Affecting Porosity Development
The incident of porosity in welding is influenced by a myriad of factors, ranging from gas securing performance to the details of welding specification setups. Welding specifications, consisting of voltage, present, travel speed, and electrode type, also impact porosity formation. The welding method employed, such as gas metal arc welding (GMAW) or secured steel arc welding (SMAW), can affect porosity formation due to variants in warmth circulation and gas insurance coverage - What is Porosity.
Impacts of Porosity on Weld High Quality
Porosity formation dramatically compromises the architectural stability and mechanical properties of bonded joints. When porosity is existing in a weld, it produces spaces or cavities within the product, lowering the general strength of the joint. These gaps function as stress and anxiety focus points, making the weld extra at risk to splitting and failing under tons. The existence of porosity likewise weakens the weld's resistance to deterioration, as the trapped air or gases within deep spaces can react with the surrounding environment, bring about deterioration over time. In addition, porosity can hinder the weld's capacity to endure pressure or influence, further threatening the overall high quality and reliability of the bonded structure. In sites essential applications such as aerospace, automobile, or architectural buildings, where safety and security and durability are vital, the harmful results of porosity on weld quality can have serious effects, emphasizing the value of decreasing porosity with correct welding techniques and procedures.
Strategies to Lessen Porosity
In addition, using the suitable welding criteria, such as the right voltage, existing, and travel speed, is crucial in stopping porosity. Maintaining a constant arc size and angle throughout welding additionally aids minimize the likelihood of porosity.

Utilizing the appropriate welding strategy, such as back-stepping or using a weaving movement, can also assist distribute warmth equally and minimize the chances of porosity development. By carrying out these techniques, welders can effectively lessen porosity and produce top notch welded joints.

Advanced Solutions for Porosity Control
Executing sophisticated innovations and cutting-edge methods plays an essential duty in achieving remarkable control over porosity in welding procedures. Additionally, using advanced welding methods such as pulsed MIG welding or changed atmosphere welding can also assist minimize porosity issues.
Another sophisticated remedy involves the use of sophisticated welding equipment. For example, using equipment with built-in functions like waveform control and innovative source of power can enhance weld quality and decrease porosity dangers. The implementation of automated welding systems with specific control over criteria can substantially decrease porosity defects.
Furthermore, integrating innovative surveillance and evaluation modern technologies such as real-time X-ray imaging or automated ultrasonic testing can assist in spotting porosity early in the welding process, permitting immediate rehabilitative activities. On the go to my site whole, incorporating these sophisticated remedies can greatly boost porosity control and improve the general quality of bonded parts.
Final Thought
In final thought, comprehending the science behind porosity in welding is important for welders and fabricators to generate top notch welds. By determining the variables influencing porosity development and applying methods to reduce it, welders can improve the total weld high quality. Advanced solutions for porosity control can better improve the welding process and ensure a solid and trusted weld. It is essential for welders to continuously enlighten themselves on porosity and carry out finest practices to achieve optimal outcomes. visit our website